Custom Case Study
The customer was evaluating technical solutions for a new automotive lithium-ion battery management system. Their two major design objectives were improving circuit efficiency and reducing the size and weight of the measurement and control systems to improve driving range and lower system costs. As this application is still relatively new, there are rapidly evolving innovations that need to be evaluated and potentially included in next-generation designs.
Typically, lithium-ion batteries operate between –30 °C and +85 °C, and accurate current measurements are critical in ensuring the correct state of charge and battery health. These measurements are usually performed using very low ohmic (typically µΩ) current shunt resistors. The specific TCR of the current shunt resistor is a reversible change of resistance as a function of temperature, and is present in all resistors. This change is non-linear, depending on the alloy materials and construction, and the actual TCR ppm varies across this wide temperature range. Taking TCR into account requires characterization across the operating temperature range to ensure accurate current measurements are recorded. In addition, temperature compensation software and circuitry are required to adjust the actual measured results for the purpose of controlling the circuit for charging and discharging.
Vishay has patented a new mechanical construction for current shunt resistors that provides current shade via an electrical obstruction that significantly reduces TCR across the operating temperature range. This “flattening” of the TCR curve down to 10 ppm/°C means real data can be recorded and used by the control circuit without requiring adjustments. The power coefficient of resistance (PCR) of the current shunt resistor is also minimized, as the effect of self-heating is significantly reduced.
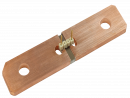
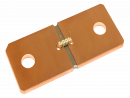
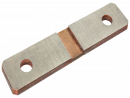
Patented shunt construction for reduced TCR (WSBE) / Standard Shunt Construction
Change in resistance over temperature due to TCR
Designing with a Vishay custom shunt resistor featuring a patented TCR construction enabled the designer to reduce the overall PCB area, component acquisition cost, and also the weight of the control circuit by eliminating the need for costly TCR compensation circuitry. Consequently, it also reduced the design time — as characterization of the circuit was no longer necessary — and also system response time by removing the need for software adjustments to the actual system current measurements during operation.
Removing this circuitry also avoids introducing errors and inaccuracies caused by the analog to digital conversion and the tolerances of the thermistor during temperature measurement, as well as any errors in the quadratic equation / mathematical models that are subsequently applied to this data. In addition, evolutionary developments for higher voltage, next-generation designs become easier and faster without the need for characterization and TCR compensation.
Please fill out the form and submit to get started.