Custom Case Study
A customer’s prototype design was developed using the Vishay RH / NH (non-inductive) series of aluminum-housed, chassis-mounted wirewound resistors. These high power resistors are typically used in high power applications that see high pulse energy, especially at start-up.
The electrical performance of the RH device met the design parameters and the PCB footprint, size, and weight requirements of the circuit. However, in application testing, the design had experienced arcing on the resistor terminal that had to be mitigated by increasing the creepage distance in the resistor. The fastest and easiest way to achieve this was to find a way to modify the existing resistor series, as this solution would not require any other changes, which are time-consuming and expensive at this stage of a design.
When contacted by the design engineer at the customer, the Vishay engineering team devised a unique solution. Special mold hooks were added to allow the mold compound to be extended onto the standard resistor terminals. This increased the creepage distance without impacting the physical dimensions of the part. After prototypes were manufactured and tested, these custom versions were supplied to the customer for application testing and were successful in passing in-house testing of the assembled system.
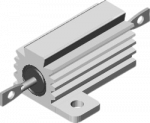
Standard RH series wirewound resistor construction
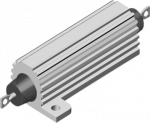
Increased creepage version (RH series) with extended terminals
By developing this solution, the customer didn’t have to redesign their boards or change product families. Both of which would have had design cost and time implications, and require additional system testing. This custom resistor, with the exception of the mold compound changes, was built upon an established standard product and therefore utilizes existing materials and manufacturing processes. As a result, the additional costs accrued to meet this design requirement were minimized.
Please fill out the form and submit to get started.